Not known Facts About Inventory Management
Wiki Article
Getting My Inventory Management To Work
Table of ContentsThe Facts About Inventory Management RevealedSee This Report about Inventory ManagementInventory Management Things To Know Before You Get ThisThe Greatest Guide To Inventory Management
There are 2 primary methods of maintaining track of supply: regular as well as perpetual. The main distinction in between these is just how often data is updated. Despite exactly how often you track stock, you might wish to utilize one of the following supply monitoring methods: ABC Evaluation, ABC (Always Better Control) Analysis is stock management that separates different products into 3 classifications based on rates and also is separated right into teams A, B, or C.The products in the B classification are reasonably less costly compared to the A classification. And also the C category has the least expensive products of all 3. EOQ Design, Economic Order Quantity is a strategy made use of for planning as well as getting an order quantity. It includes making a choice pertaining to the amount of stock that need to be put in supply at any type of provided time. Inventory Management.
FSN Technique, This approach of supply control refers to the process of monitoring all the products of supply that are not used often or are not called for at all times. They are after that classified right into 3 different groups: fast-moving inventory, slow-moving inventory, and also non-moving inventory. JIT Method, In the nick of time inventory control is a process used by suppliers to control their inventory levels.

The 6-Second Trick For Inventory Management
VED Evaluation, VED is a strategy utilized by organizations to control their stock. The high level of inventory that is needed for production normally justifies the low stock for those components.Wrike is a job management option that can assist you do specifically that. With Wrike's item management devices, you can handle all of your item team's activities in one place as well as get one of the most out of every project. Wrike's product launch automation aids accelerate product launches with a streamlined strategy.
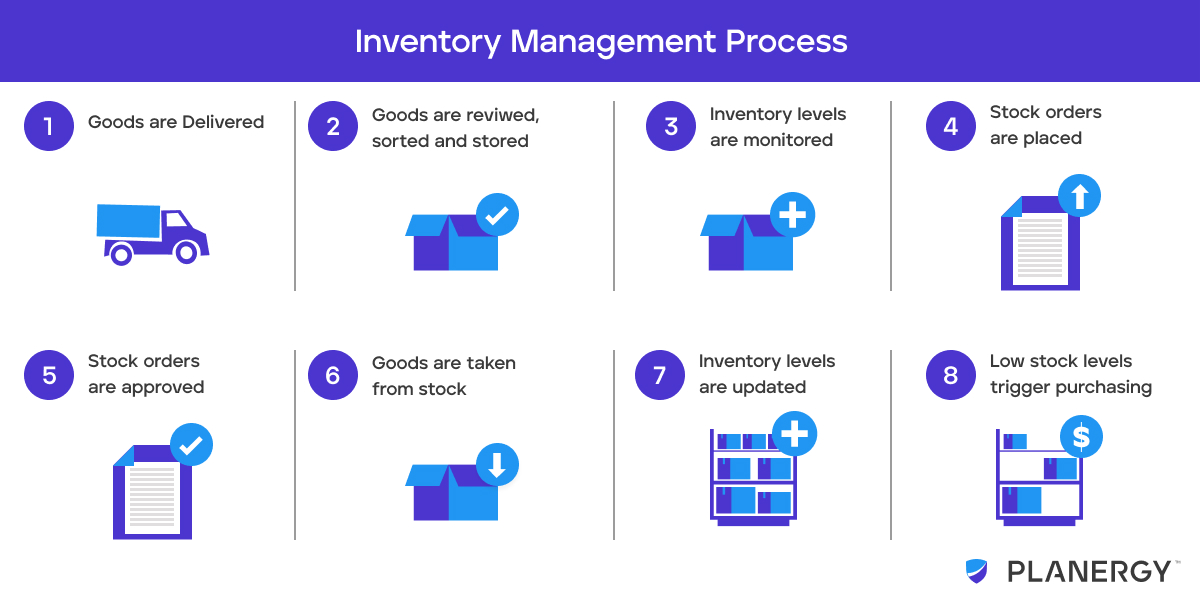

See This Report about Inventory Management
Stock management describes the procedure of buying, saving, making use of, as well as offering a company's supply. This consists of the administration of resources, elements, and ended up products, as well as warehousing as well as handling of such products. There are various sorts of stock management, each with its advantages and disadvantages, depending on a business's needs.Supply administration attempts to efficiently simplify inventories to prevent both gluts as well as lacks. Four significant inventory administration approaches include just-in-time monitoring (JIT), products demand preparation (MRP), financial order quantity (EOQ), and days sales of supply (DSI). There are benefits and drawbacks per of the techniques, evaluated below. A firm's supply is just one of its most useful properties.
A shortage of stock when and also where it's needed can be incredibly destructive (Inventory Management). At the exact same time, inventory can be believed of as an obligation (otherwise in an accountancy sense). A huge stock lugs the threat of perishing, theft, additional reading damages, or shifts in need. Stock should be guaranteed, and also if it is not marketed in time it might have to be taken care of at clearance pricesor simply ruined.
Tiny companies will certainly typically keep track of stock by hand as well as identify the reorder factors and amounts making use of spreadsheet (Excel) solutions.
Get This Report on Inventory Management
Proper inventory monitoring strategies vary depending on the market. An oil depot is able to store big amounts of supply for prolonged durations of time, allowing it to wait on demand to grab. While storing oil is pricey as well as riskya fire in the U.K. in 2005 resulted in numerous extra pounds in damage and also finesthere is no danger that the inventory will spoil or go out of design.For companies with complicated supply chains and also manufacturing procedures, balancing the dangers of inventory gluts as well as lacks is especially tough. To attain these equilibriums, companies have actually established numerous techniques for supply administration, consisting of just-in-time (JIT) and materials requirement preparation (MRP). Some companies, such as monetary services firms, do not have physical stock therefore needs to count on solution procedure administration.
Supply has to be literally counted or determined before it can be placed on a balance sheet. Companies generally keep sophisticated inventory management systems efficient in tracking real-time stock degrees. Stock is represented utilizing among 3 methods: first-in-first-out (FIFO) setting you back; last-in-first-out (LIFO) setting you back; or weighted-average setting you back. A supply account normally is composed of 4 separate classifications: Resources represent various materials a firm purchases for its production process.
Job in procedure (likewise check it out referred to as goods-in-process) stands for raw materials in the process of being transformed right into a finished item. Ended up goods are finished products easily available offer for sale to a business's consumers. Product stands for completed goods a company purchases from a provider for future resale. Depending upon the kind of company or product being assessed, a business will certainly utilize various supply monitoring techniques.
Report this wiki page